Challenges of Developing Small Scale Thermal Hydrolysis and Digestion Projects
Panter K., Holte, H.R., Walley, P.
18th European Biosolids & Organic Resources Conference & Exhibition, 2013
Abstract
The Thermal Hydrolysis Process (THP) as a pre-treatment for anaerobic digestion (AD) was first explained at the European Biosolids conference in 1997. Since then THP has become a standard process in UK and Ireland with over 20% of all sludge being treated this way. These projects are in the 300,000 to 3 million PE range. The challenge has been to make economical systems for smaller digestion projects without losing system efficiency or reliability.
In designing smaller systems for the 100,000 to 300,000 p.e. range, the following factors were considered as essential to retain system efficiency: maintaining batch action in the continuous process; using steam injection not heat exchangers; maintaining heat recovery using a pre-heat tank for energy efficiency; optimum dry solids feed; ability for flash steam explosion; smooth steam profile for waste heat use; maintain high availability.
In designing smaller systems the following factors were considered important in keeping installed cost down: standardising design for assembly line production; fitting the systems in a standard ISO container footprint; rapid installation for minimum project and site costs.
The new systems are based on 6m3 and 2 m3 reactors rather than 12 m3, but the operating method is identical to larger systems but at a much reduced cycle time. The batch can still be up to 30 minutes and has the benefit of being self cleaning compared to continuous systems at the same high dry solids.
The new system is to be installed in a number of projects in the UK and elsewhere. Examples of size and scope are given.
Download the paper.
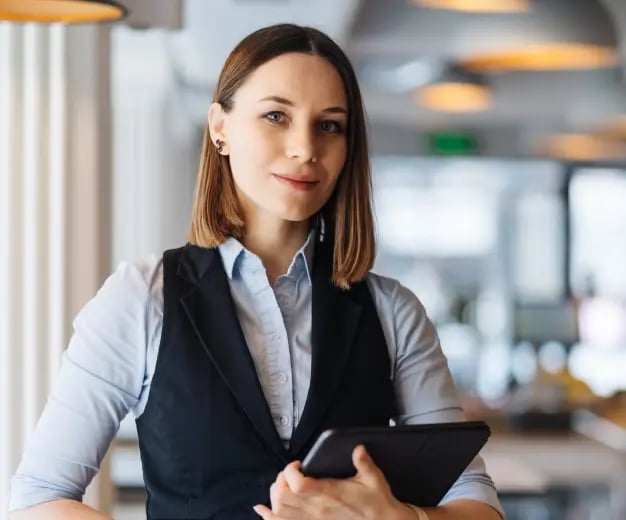
Write your own success story
Seen what we've done for others? Let’s chat about how we can do the same for you. Get in touch with our team to learn how thermal hydrolysis can transform your plant, too.